The automated spray painting system with conveyor technology marks a revolutionary advancement in industrial painting processes, boasting heightened efficiency and precision. In an era where speed and quality dictate market leadership, businesses are increasingly turning to this innovation, redefining traditional painting methods.

As someone with extensive experience in evaluating industrial equipment, I've seen first-hand the transformational impact this technology has on manufacturing and production lines. A system like this, equipped with automated controls, minimizes human error, which traditionally could result in uneven coatings or paint wastage. By standardizing the painting process, this technology ensures consistency across all products, a critical factor in maintaining high quality and reducing costs associated with material wastage or product re-runs.
From an expertise stance,
the integration of a conveyor system within an automated spray painting setup significantly boosts production throughput. Conveyors seamlessly synchronize with robotic arms, timing the precise moment for paint application, which is unachievable by manual setups. The built-in sensors and data-driven analytics facilitate real-time adjustments, ensuring optimal paint thickness and uniform application, regardless of product shape or size.
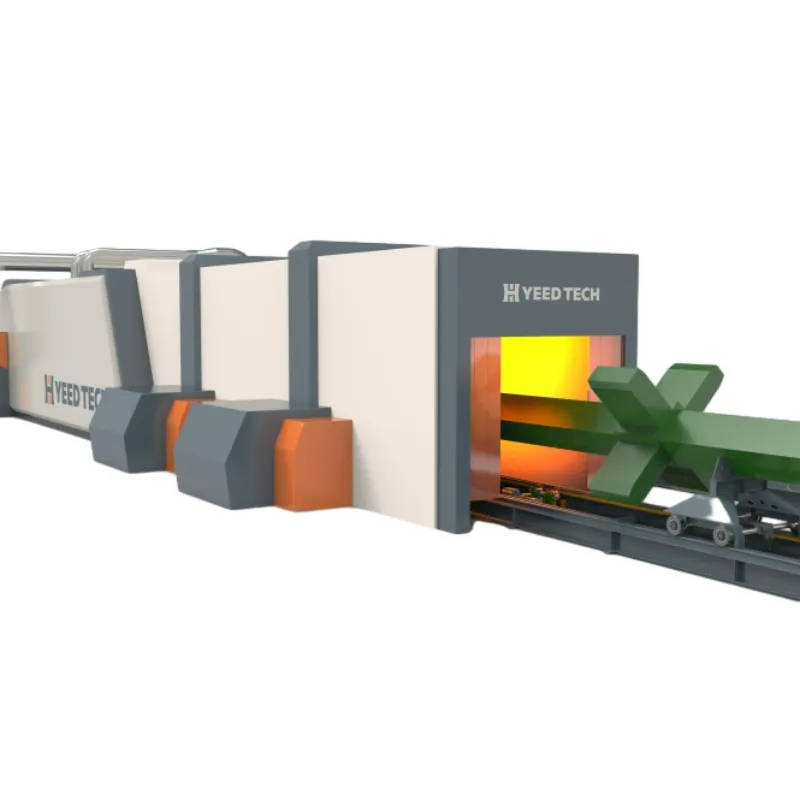
Authoritative sources within the manufacturing sector cite numerous case studies where companies have observed a reduction in lead time by up to 60%. Such enhancements in efficiency are largely credited to the continuous flow of products enabled by conveyors, alongside the adaptability of spray systems to switch between different paint types and colors without downtime.
sistema automático de pintura por pulverización con transportador
Trustworthiness is fortified by the consistent performance of these systems. The precision of automated spray systems with conveyors leads to less overspray and a cleaner working environment, contributing to sustainable practices and improving compliance with increasingly stringent environmental regulations. Manufacturers report not only improved product aesthetics but also longer-lasting finishes due to superior paint adhesion, a confidence booster for brands looking to promise enhanced product durability to end consumers.
Looking ahead, this technology promises even more sophisticated developments. Integration with AI and machine learning algorithms could enable predictive maintenance, further enhancing reliability and reducing unexpected downtimes. Moreover, the scope for innovation in paint formulations, tailored to work seamlessly with these advanced systems, opens exciting avenues for businesses aiming for eco-friendly solutions without compromising on quality.
One cannot overlook the importance of skilled professionals in harnessing the full potential of automated spray painting systems. Training programs and certifications are crucial, ensuring that operators are not only familiar with the newest features but also compliant with safety and efficiency standards. Such measures guarantee that the deployment of these systems in a factory setting confirms to all relevant guidelines, maintaining a trusted production environment.
In conclusion, investing in an automated spray painting system with conveyor technology is no longer an optional upgrade but a strategic necessity for manufacturers. This investment in technology not only ensures immediate operational benefits but also secures long-term competitive advantages through innovation, consistent quality, and enhanced reputability in the market.