Understanding the cost of structural steel painting involves more than just purchasing paint and hiring labor. It's an intricate process that melds material quality, labor expertise, environmental conditions, and project specifications. Careful consideration of each aspect ensures you not only achieve a durable finish but also maintain fiscal responsibility throughout your construction project.
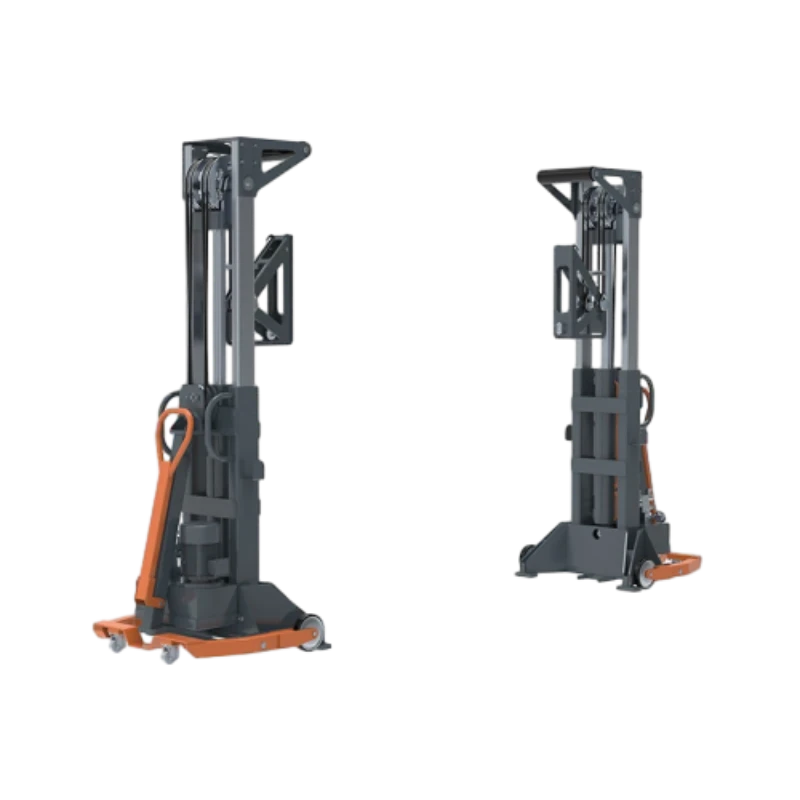
The initial step in determining the cost involves selecting the right type of paint. Structural steel requires coatings that resist corrosion, weathering, and sometimes even fire. Epoxy paints and polyurethane are popular choices due to their durability and protective qualities. While these may be more expensive than standard paints, their longevity and performance can lead to cost savings in the long run by reducing the frequency of maintenance reapplications.
Labor constitutes a significant portion of the painting cost. Skilled professionals who are experienced in handling structural steel bring accuracy and efficiency to the job that unskilled labor cannot. Experienced painters reduce waste, ensure proper adhesion, and apply coatings evenly to prevent weaknesses in the protective layer. Ideally, hiring a certified contractor who adheres to safety standards not only guarantees quality work but also minimizes potential risks, further enhancing the project's cost-effectiveness.
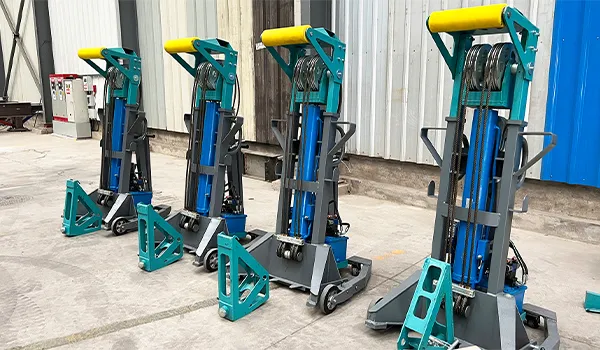
Project size and complexity play a crucial role in shaping the overall cost. Larger structures require more materials and labor hours, which automatically elevates the budget. Complex shapes with many angles or structures located in challenging environments demand specialized equipment and additional time, thereby increasing expenses. Accurate measurement and assessment of the structure can provide a realistic estimate, helping allocate the appropriate budget from the onset.
Environmental conditions must be factored into the cost calculation as well. The application of paint on structural steel is sensitive to temperature, humidity, and weather conditions. Unfavorable conditions can delay projects, requiring the use of accelerators or temporary shelters, which introduces additional costs. Understanding the local weather patterns and selecting the optimal time for painting can mitigate these potential expenses and ensure a smooth workflow.
costo de pintura de acero estructural
Surface preparation is another critical factor impacting cost. Clean and properly prepared surfaces ensure maximum paint adhesion and longevity, but they demand time and resources. Methods such as sandblasting or power washing remove rust, dirt, and old paint effectively but add to the initial expense. However, investing in thorough surface preparation prevents adhesion failures and extends the life of the coating, providing long-term savings.
Regular maintenance should not be overlooked when considering the painting cost of structural steel. Planning for future inspections and touch-ups can stave off extensive repairs, which are costly and disruptive. Implementing a maintenance plan that includes regular checks and minor repairs as needed will ensure the integrity of the coating and the underlying steel. Although this extends the budget beyond initial application costs, it safeguards against more significant expenditures associated with corrosion.
Engaging with experts in the field, such as experienced contractors or coating specialists, contributes significantly to controlling costs. Their insights help choose the right materials, recommend proven techniques, and provide project management tips that keep your budget in check. Their reputation and reliability stand as a testament to the quality and trust needed in a successful project.
Overall,
calculating the cost of painting structural steel is a multifaceted endeavor. It requires upfront planning, a comprehensive understanding of materials and techniques, and acknowledgment of ongoing maintenance needs. By investing wisely in labor, quality materials, and expert advice, the initial expenditure can ultimately lead to savings through reduced maintenance and extended structural life, enhancing the project's E-A-T and ensuring its success in both performance and financial perspectives.