In the rapidly evolving world of construction and manufacturing, the integration of steel structure fully automatic manufacturing equipment has emerged as a game-changer, providing unprecedented benefits in terms of efficiency, precision, and cost-effectiveness. This cutting-edge technology is reshaping the landscape of the construction industry, offering a plethora of advantages that are critical for every construction firm aiming to stay ahead in a competitive market.
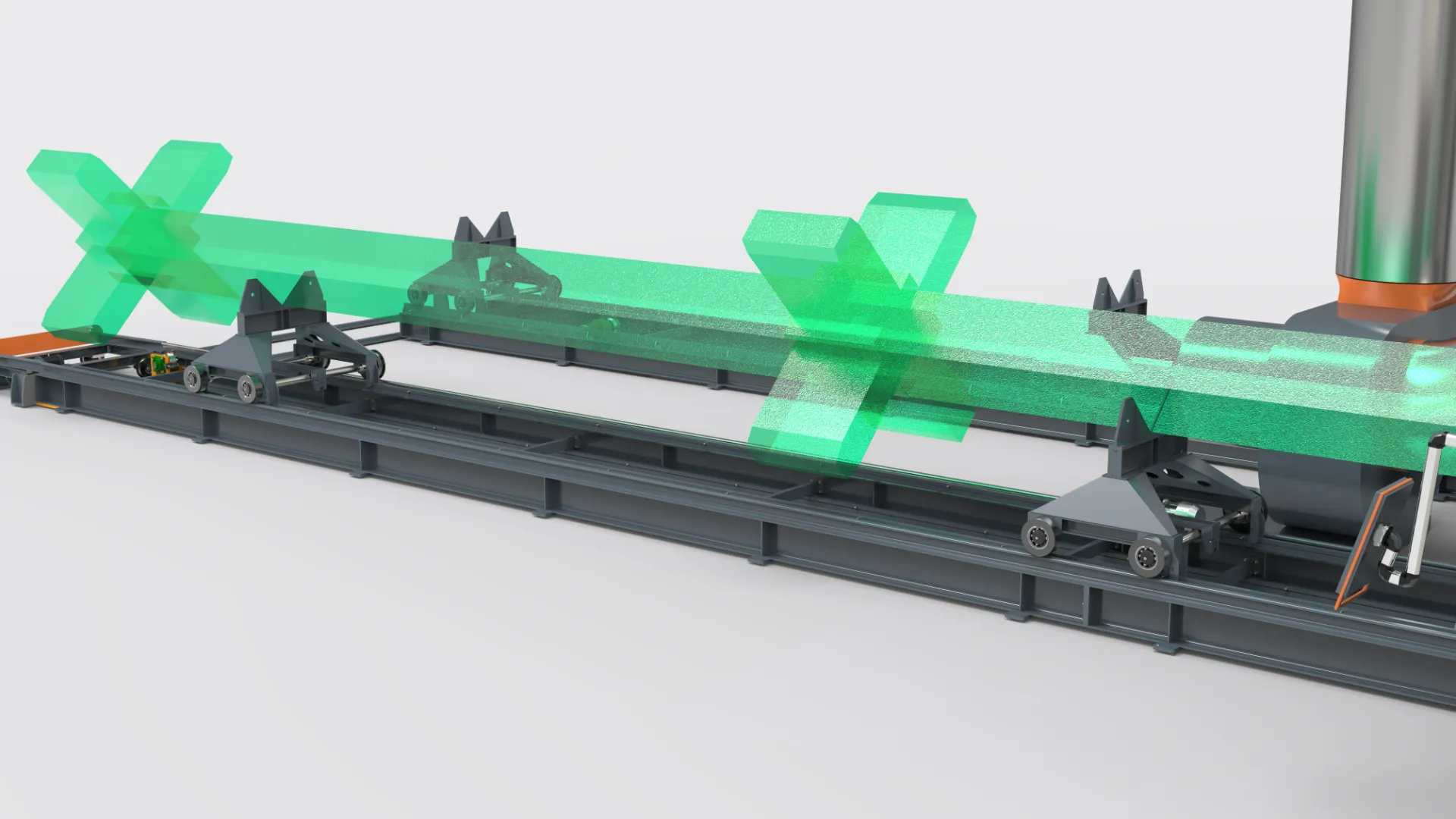
One of the most remarkable experiences shared by companies utilizing fully automatic manufacturing equipment for steel structures is the significant reduction in production time. Traditional methods, reliant on manual labor and semi-automatic machines, often led to delays and inconsistencies. However, with fully automatic systems, manufacturers can achieve streamlined operations that enhance overall productivity. Automated systems can perform complex tasks with remarkable precision, minimizing human error and ensuring that all components meet rigorous quality standards.
From an expertise standpoint, the deployment of steel structure fully automatic manufacturing equipment requires a deep understanding of both the technology and the materials involved. Professionals in this field must be adept at integrating advanced software with precise mechanical processes. This equipment often incorporates state-of-the-art technologies such as Computer Numerical Control (CNC) systems, robotics, and real-time monitoring, which collectively ensure that each phase of production is optimized for accuracy and efficiency.
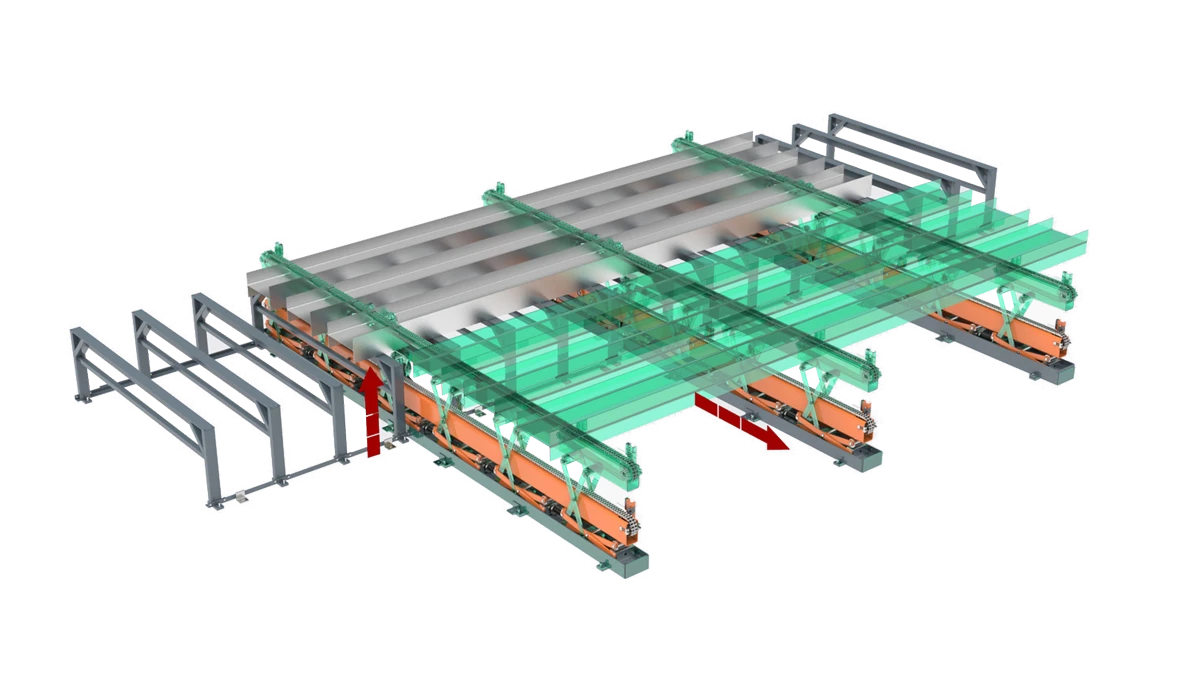
The authoritativeness of fully automatic manufacturing equipment for steel structures is bolstered by its ability to consistently deliver high-quality products. This consistency is vital in maintaining structural integrity, crucial for safety and durability in construction projects. As a result, many leading industry bodies and construction standards organizations endorse these systems for their ability to produce components that comply with stringent regulatory requirements. This endorsement serves as a testament to the reliability and effectiveness of automated systems in the manufacturing of steel structures.
steel structure fully automatic manufacturing equipment
Trustworthiness is an essential aspect of any new technology, and fully automatic systems hold a robust reputation for reliability and performance. Users frequently report enhanced confidence in project outcomes, knowing that the equipment can handle complex tasks with minimal risk of malfunction. This trust is built on the equipment’s ability to deliver precise results within tight tolerances, thus reducing the likelihood of costly rework and project delays.
Furthermore, automatic manufacturing systems in steel structure fabrication offer considerable environmental benefits. These systems are typically more energy-efficient than their manual counterparts, as they can optimize resource usage and minimize waste. By reducing scrap material and promoting the recycling of steel off-cuts, these systems contribute to more sustainable construction practices. Such advancements play a critical role in helping the industry meet increasingly stringent environmental regulations and sustainability goals.
In summary,
the incorporation of steel structure fully automatic manufacturing equipment represents a significant leap forward in the construction industry. Companies adopting this technology not only experience enhanced production efficiency and product consistency but also position themselves as leaders in sustainable and innovative manufacturing practices. Those who embrace this technological advancement are well-equipped to meet the challenges of modern construction, ensuring their competitiveness and profitability in the marketplace. As the industry continues to evolve, the expertise, authoritativeness, and trustworthiness of fully automatic systems will undoubtedly serve as a cornerstone for future developments, driving further innovation and setting new standards for quality and efficiency.