Understanding the cost per square foot for Pre-engineered Building (PEB) structures is crucial for stakeholders in the construction sector. These structures are gaining traction worldwide due to their cost-effectiveness, expedited construction timelines, and enhanced design flexibility. However, calculating their cost per square foot requires a nuanced approach, considering multiple variables that impact the final pricing.
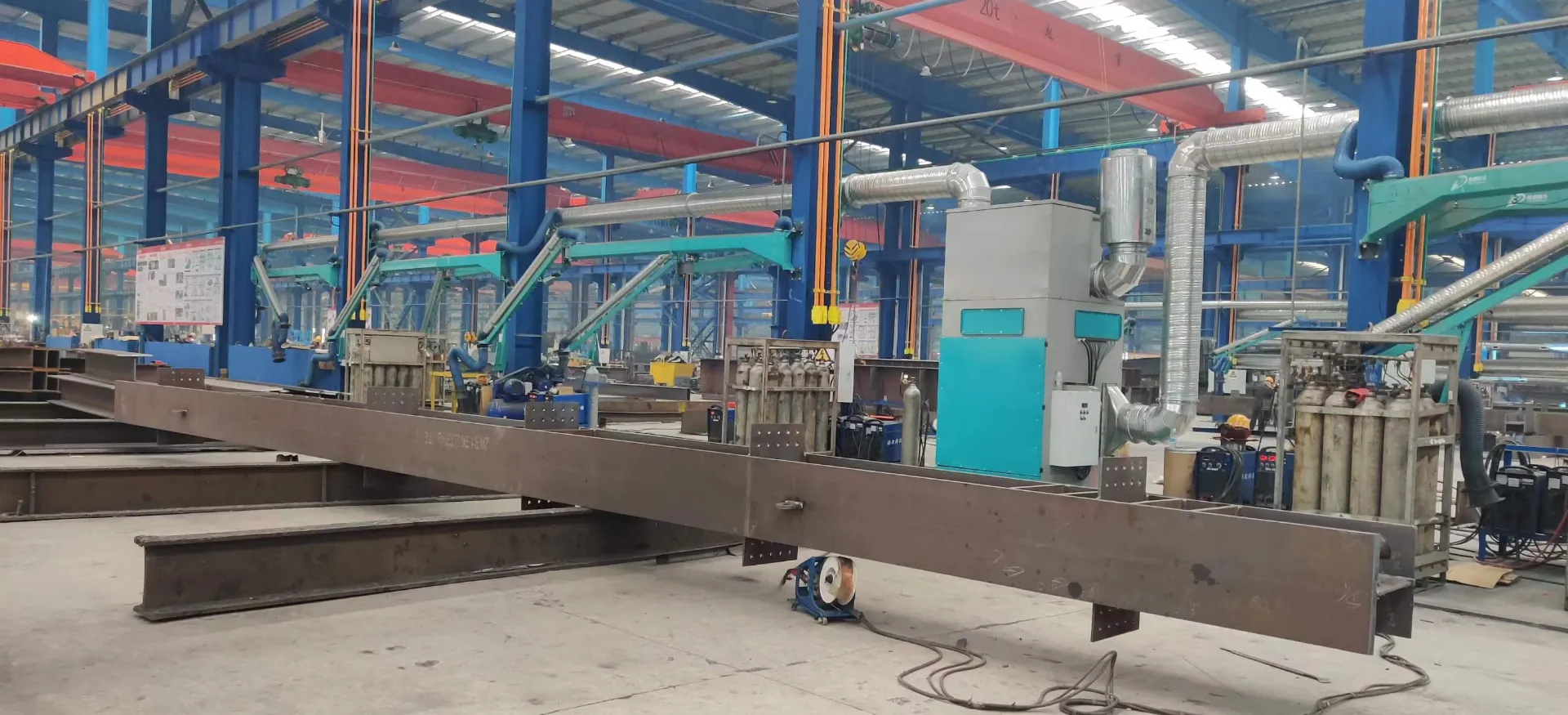
Ensuring a comprehensive understanding starts with distinguishing between direct and indirect costs. Direct costs encompass materials like steel, panels, insulation, and accessories. Typically, the grade of steel used is a significant determiner; higher grades offer more strength and longevity but at a greater price. Additionally, the choice of panels—whether insulated, galvanized, or painted—further influences pricing. Insulation type also affects cost, varying with choices like fiberglass, rock wool, and polyurethane.
Furthermore, indirect costs must not be neglected. These include transportation, design fees, labor, site preparation, and potential permits. The geographical location can dramatically alter these expenses, as urban regions often incur higher fees due to logistical challenges and labor rates. In contrast, rural areas might benefit from lower wages and permit flexibility.
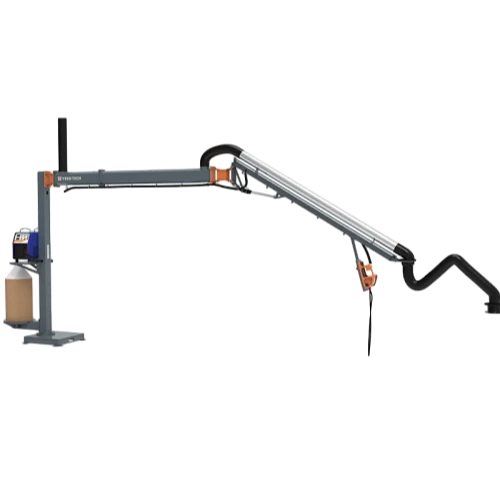
One crucial aspect affecting PEB structure costs is the architectural complexity. A straightforward rectangular building is naturally more cost-effective due to its simplicity in design and construction. On the other hand, tailored designs with intricate features or multiple levels may require additional engineering efforts, specialized materials, and skilled labor, thereby inflating costs.
Weather and environmental demands also need consideration. In areas subjected to extreme weather conditions, structures must be designed for higher durability, necessitating superior materials and engineering, which directly increase costs per square foot. Additionally, regulatory compliance for environmental standards can further inflate the budget with the integration of green technology or materials for sustainability.
Experience and expertise in construction management play pivotal roles in managing costs efficiently. Partnering with experienced contractors who specialize in PEB structures can lead to cost savings. These professionals bring authority and a reliable track record, allowing for more accurate cost predictions and resource allocations, leading to minimized waste and enhanced efficiency.
peb structure cost per sq ft
A tangible experience from a recent industrial PEB project highlights these principles in action. The project, a 50,000-square-foot warehouse, initially faced a budget overrun due to underestimation of loading capacity requirements. Upon consulting with a seasoned structural engineer, the project team opted for a higher grade of steel, ensuring structural integrity without excessive material surplus. This informed decision, though initially more expensive per unit, ultimately provided savings by preventing costly post-completion modifications.
Trust plays an integral role when navigating PEB structure costs. Ensuring that every stakeholder—from designers to construction workers—communicates effectively and honestly can prevent misunderstandings that might cause unexpected expenses. Transparency with suppliers regarding material sourcing and costs also lends itself to trustworthiness, fostering a reliable partnership that benefits all parties involved.
PEB structures offer cost advantages over traditional construction methods by significantly reducing material waste and labor time. Additionally, ongoing technological improvements in design software and materials continue to enhance their cost-competitiveness. Such innovations allow for more precise calculations, optimized designs, and streamlined operations, consistently lowering the cost per square foot in the long term.
Investors and developers need to weigh the benefits of PEB structures against upfront costs meticulously. Long-term savings from reduced maintenance, energy efficiency, and quick deployment can often outweigh initial expenditures. Moreover, PEB structures' adaptability to future expansions adds a layer of economic efficiency, making them an attractive investment in various sectors from industrial to commercial applications.
In conclusion, understanding the costs involved in constructing PEB structures is a multi-faceted endeavor. By emphasizing experience, expertise, authority, and trustworthiness, investors and builders can navigate these factors adeptly, ensuring projects are delivered within budget without compromising quality or performance. Adopting a strategic, informed approach is key to realizing the full economic potential of PEB solutions, paving the way for innovative, sustainable development in the modern construction landscape.