Automated spray painting systems with conveyors have revolutionized the industrial painting process, significantly enhancing efficiency and product quality. This technology is an essential component for manufacturers aiming to optimize their production line while ensuring consistent paint application. Understanding the intricacies of these systems can provide companies with a competitive edge.
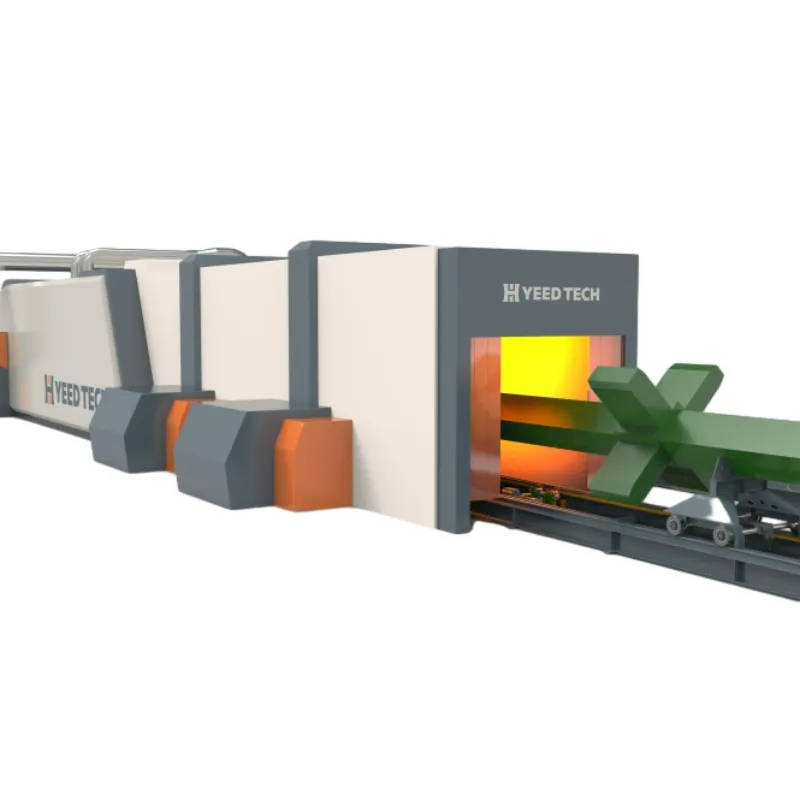
Utilizing a conveyor system in automated spray painting eliminates many pitfalls associated with manual painting methods. The use of conveyors ensures a continuous and uniform movement of products through the spray zone, allowing for a precise and even coating. This capability not only reduces material wastage but also minimizes human error, ensuring a consistently high-quality finish across all units.
The core of this advanced system is the mechanized arm equipped with precision spray nozzles, which are controlled by sophisticated software. These systems can be calibrated to apply various types of paint and coatings, covering an extensive range of textures and finishes. By incorporating variable speed controls and programmable paths, the system can adapt to paint different shapes and sizes of products without requiring significant manual adjustments, offering unparalleled flexibility and efficiency.
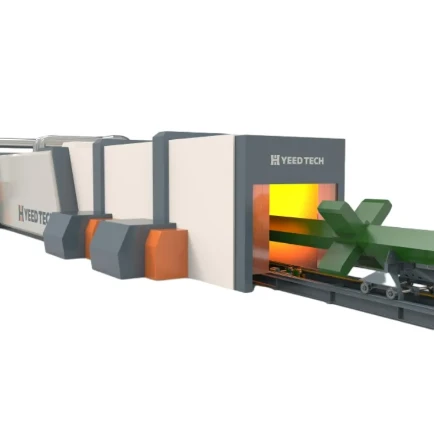
A key advantage of an automated spray system with a conveyor is its ability to operate continuously, significantly increasing throughput. This continuous operation means that production lines can run around the clock, meeting higher output demands without compromising on quality. Furthermore, automation dramatically reduces labor costs and operational downtime associated with manual painting processes, translating into substantial cost savings for manufacturers.
sistem lukisan semburan automatik dengan penghantar
Safety is another critical factor where automated spray systems excel. Traditional manual painting methods pose several risks, including exposure to hazardous chemicals and ergonomically challenging tasks. Automatization of the spray painting process ensures that workers are not exposed directly to harmful fumes and minimizes repetitive motion injuries. Modern systems are equipped with advanced ventilation and filtration units that effectively manage overspray and volatile organic compounds (VOCs), ensuring compliance with stringent environmental and health regulations.
For businesses seeking to implement an automated spray painting system, selecting the right equipment is crucial. Factors such as the size of the production facility, the specific types of products being painted, and the desired finish quality must be considered. Collaborating with reputable manufacturers who offer customizable solutions can help tailor the system to meet specific production needs, ensuring optimal performance and return on investment.
Moreover, integrating an automated spray painting system with conveyors into an existing production line requires careful planning. It is advisable to work with experts in industrial automation who can offer insights into the setup and maintenance of these systems. Proper training for staff members on operating and troubleshooting equipment guarantees seamless integration and operational continuity.
In conclusion, the adoption of automated spray painting systems with conveyors represents a strategic investment for manufacturers looking to enhance their production capabilities. By leveraging this technology, businesses can achieve higher productivity, improved quality, and greater safety standards, all while maintaining cost-effectiveness. It is this combination of benefits that underscores the authority and reliability of automated spray systems as a cornerstone of modern industrial manufacturing.